Montaj Doğruluğunu Sağlama Yöntemleri Nelerdir?
Konumlandırma hatasını hesaplama yöntemleri nelerdir?
İki açıdan konumlandırma hatası:
1. İş parçası konumlandırma yüzeyinin veya fikstür üzerindeki konumlandırma elemanının hatalı olmasından kaynaklanan konumlandırma hatasına referans konum hatası denir.
2. İş parçasının proses verisi ve konumlandırma verisinden kaynaklanan konumlandırma hatasına veri uyumsuzluğu hatası denir.
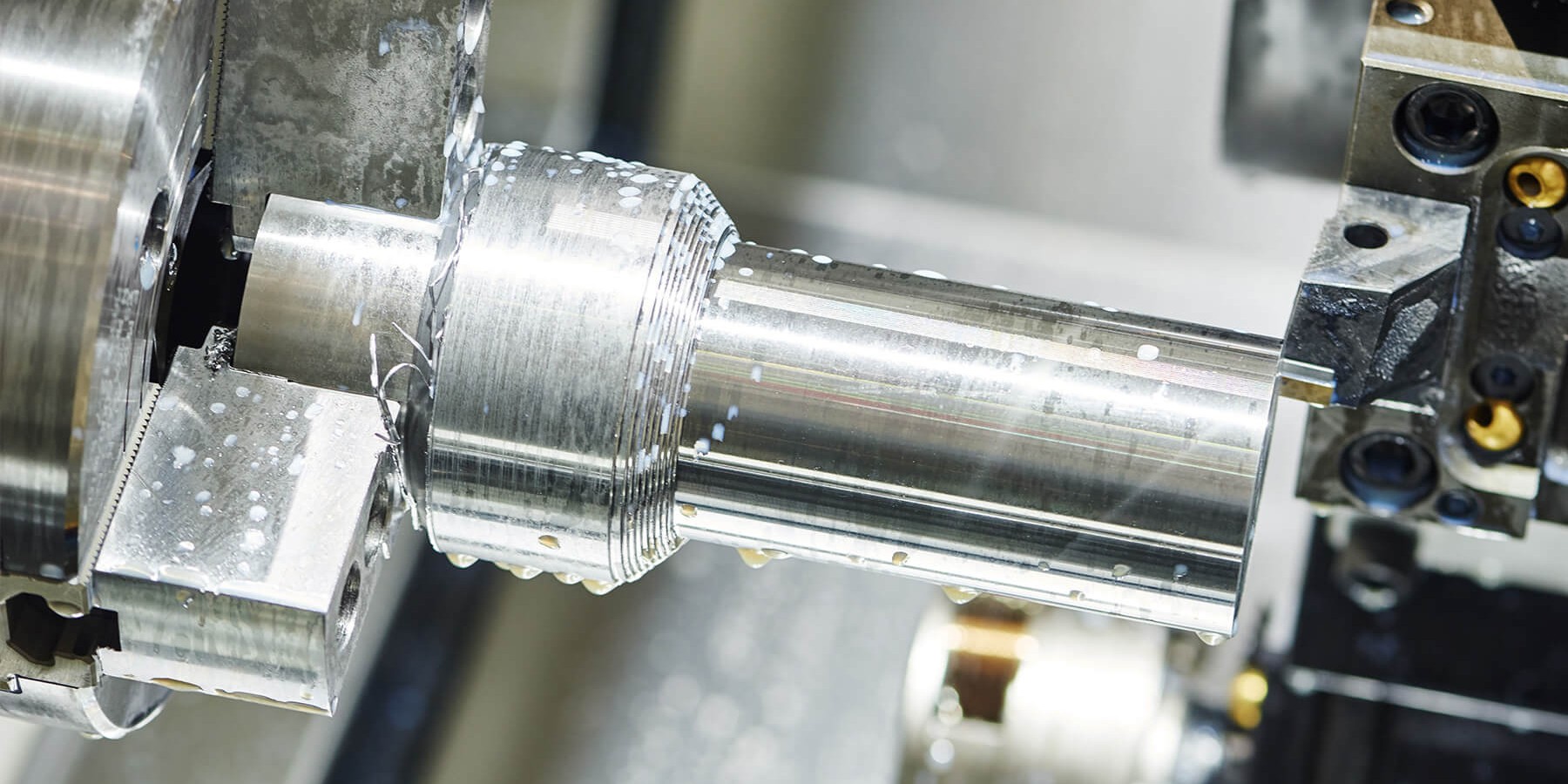
İş parçası sıkıştırma cihazının tasarımı için temel gereksinimler.
1. Sıkıştırma işleminde, iş parçasının doğru konumda elde edilen konumunu koruyabilmelidir.
2. Sıkıştırma kuvvetinin boyutu uygundur, sıkma mekanizması, iş parçasının işleme sürecinde gevşeme veya titreşim üretmemesini sağlamalı, aynı zamanda iş parçasında uygunsuz deformasyon ve yüzey hasarını önleyebilmelidir, sıkma mekanizması genellikle kendinden kilitlemeli olmalıdır
3. Sıkıştırma cihazının kullanımı kolay, emek tasarrufu sağlayan ve güvenli olmalıdır. 4. Sıkıştırma cihazının karmaşıklığı ve otomasyonu, üretim hacmi ve üretim modu ile orantılı olacaktır. Yapısal tasarım basit, kompakt olmalı ve mümkün olduğunca standartlaştırılmış bileşenleri benimsemelidir.
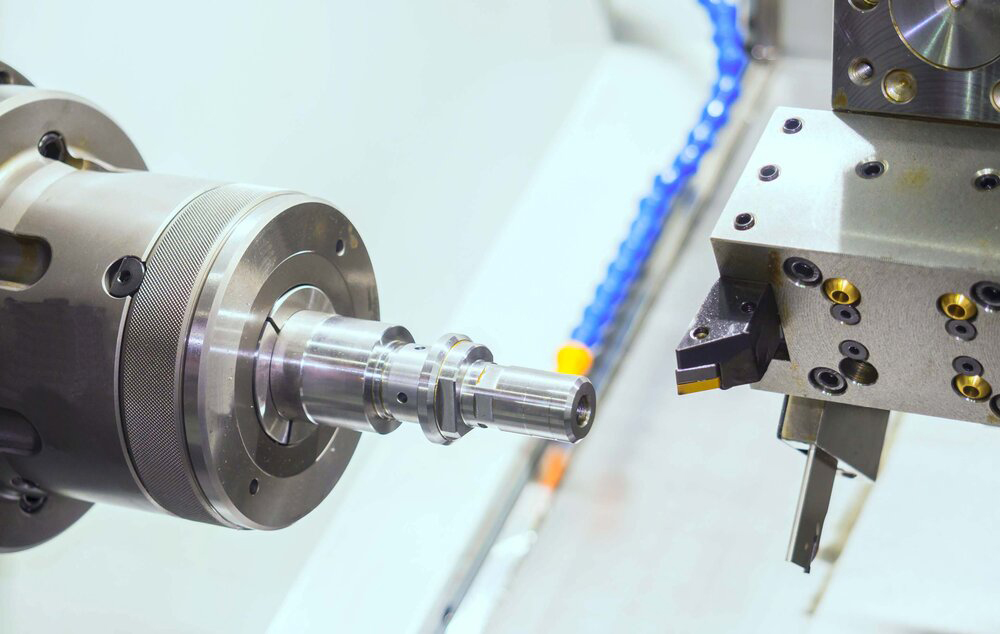
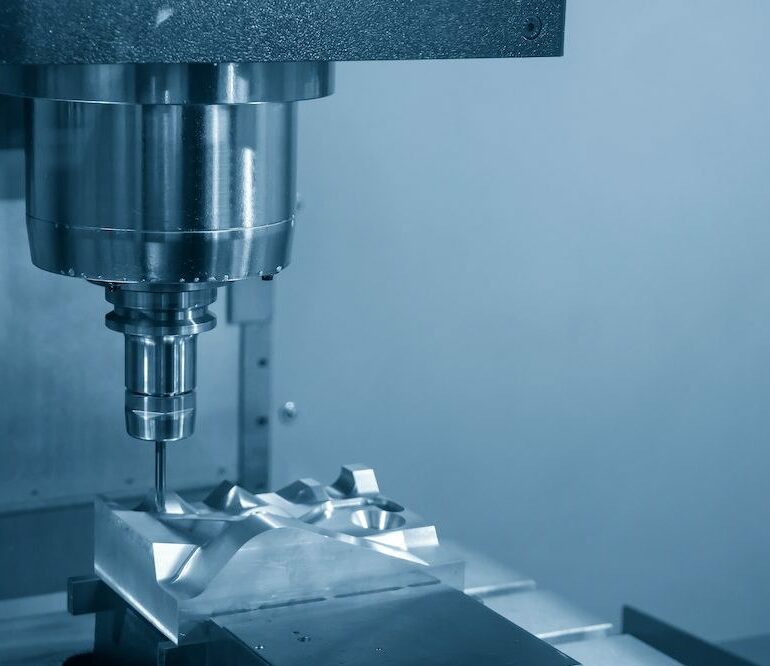
Sıkıştırma kuvvetini belirlemek için üç unsur? Sıkıştırma kuvvetinin yönünü ve noktasını seçmenin ilkeleri nelerdir?
Boyut yönünün kenetleme kuvveti yönünün seçimi genel olarak aşağıdaki ilkelere uygun olmalıdır:
1. Sıkıştırma kuvvetinin yönü, konumlandırmaya zarar vermeden iş parçasının doğru konumlandırılmasına yardımcı olmalıdır, bu nedenle genel gereksinim, ana sıkıştırma kuvvetinin konumlandırma yüzeyine dik olmasıdır.
2. Sıkıştırma kuvvetinin yönü, iş parçası sıkıştırma deformasyonunu azaltmak için mümkün olduğunca iş parçasının büyük sertliğinin yönüyle tutarlı olmalıdır.
3. Gerekli sıkma kuvvetini azaltmak için sıkma kuvvetinin yönü, kesme kuvveti, iş parçası yerçekimi yönü ile mümkün olduğu kadar fazla olmalıdır. Sıkma kuvveti noktası seçimi genel prensipler:
1) iş parçasının sabit konumlandırılmasını sağlamak için sıkma kuvveti noktası, destek elemanı tarafından oluşturulan destek yüzeyinde olmalıdır
2) iş parçasının sıkma deformasyonunu azaltmak için sıkma kuvveti iyi sertlikte olmalıdır
3) İş parçası üzerinde kesme kuvvetinin neden olduğu dönme momentini azaltmak için sıkma kuvveti işleme yüzeyine mümkün olduğunca yakın olmalıdır.
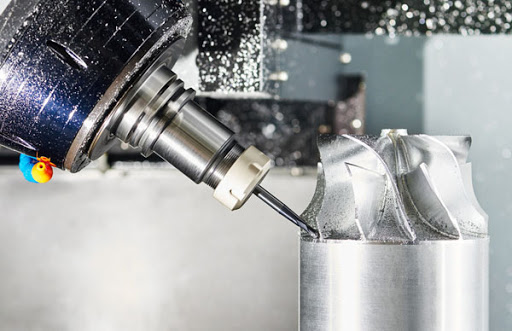
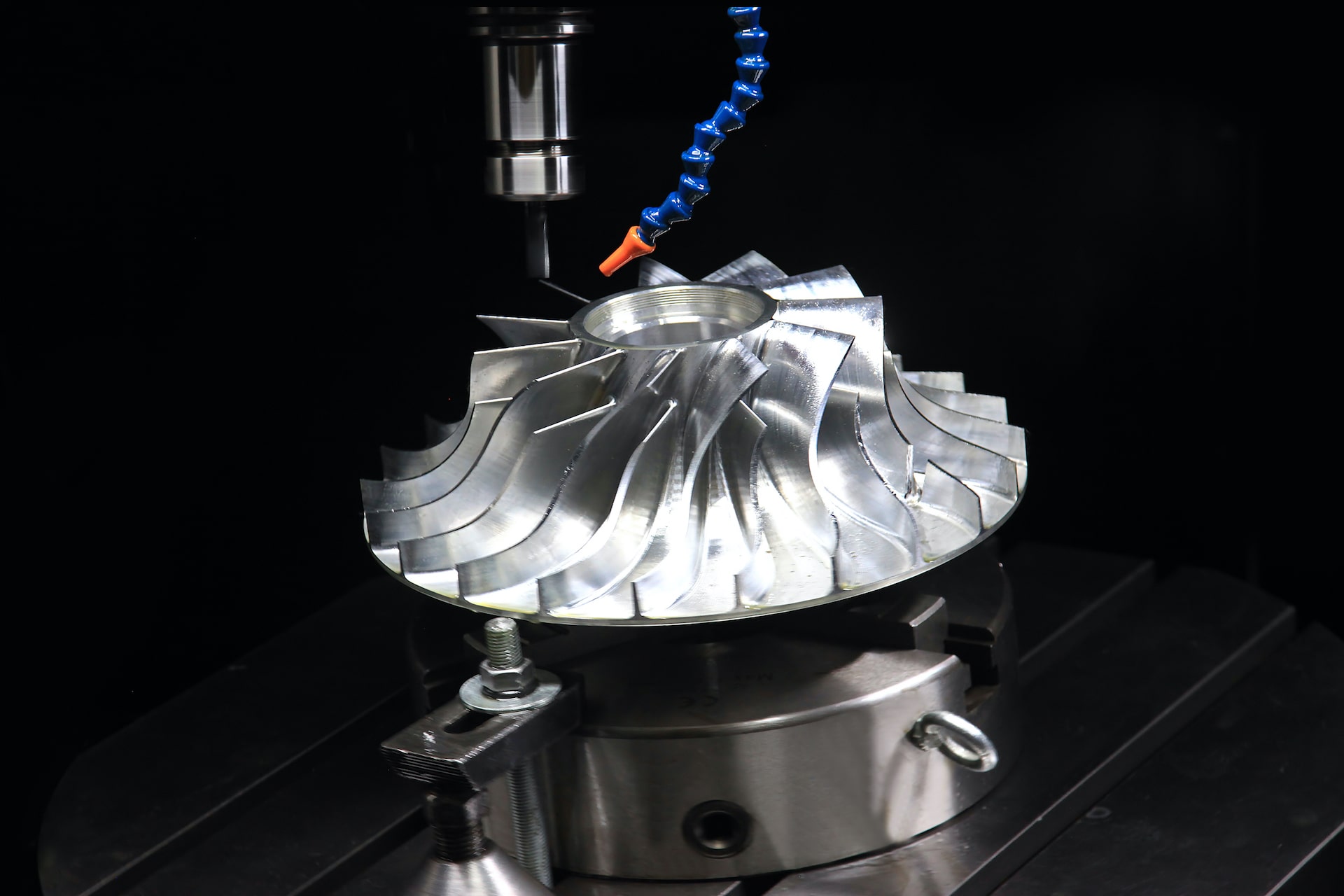
Yaygın olarak kullanılan sıkıştırma mekanizmaları nelerdir?
Eğimli kamalı kenetleme mekanizmasının analizine ve kavranmasına odaklanın.
- Eğimli kama sıkma yapısı
- Vida sıkma yapısı
- Eksantrik sıkma yapısı
- Menteşe sıkma yapısı
- Merkezleme sıkma yapısı
- Bağlantı sıkma yapısı
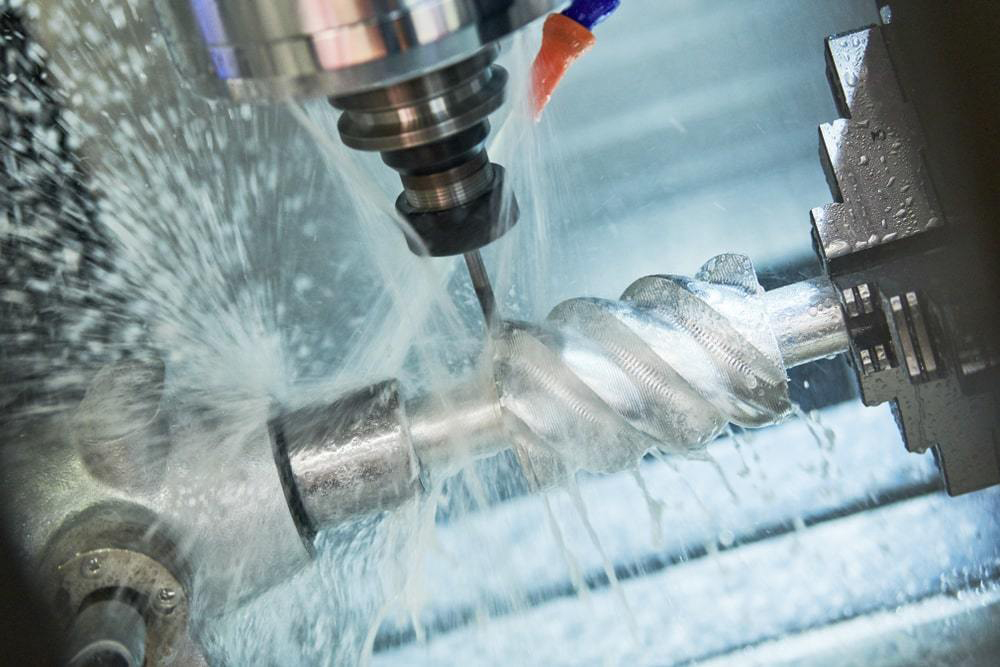
Matkap kalıbının yapı özelliklerine göre nasıl sınıflandırılır? Matkap manşonunu yapısal özelliklerine göre nasıl sınıflandırabiliriz? Matkap şablonuna ve klipse özel bağlantı şekline göre hangi birkaç çeşide ayrılır?
Sondaj kalıbının ortak yapı özelliklerine göre:
- Sabit delme kalıbı
- Döner matkap kalıbı
- Fip matkabı
- Kapak plakası delme kalıbı
- Sürgülü kolon tipi sondaj kalıbı sondaj kalıbı yapısı özellikleri sınıflandırması:
- Sabit delme kalıbı
- Delme kalıbını değiştirebilir
- Matkap kalıbını hızla değiştirin
- Özel bağlantı modunun klipsindeki özel delme kalıbı delme şablonu: sabit menteşe tipi, ayrılmış asılı tip.